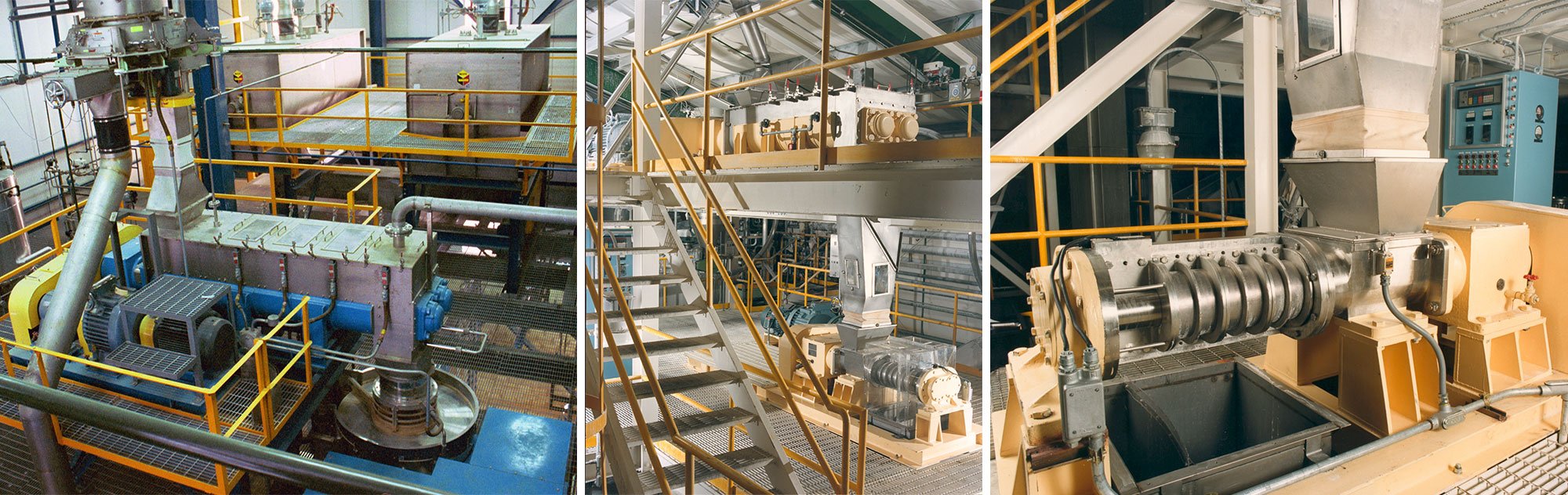
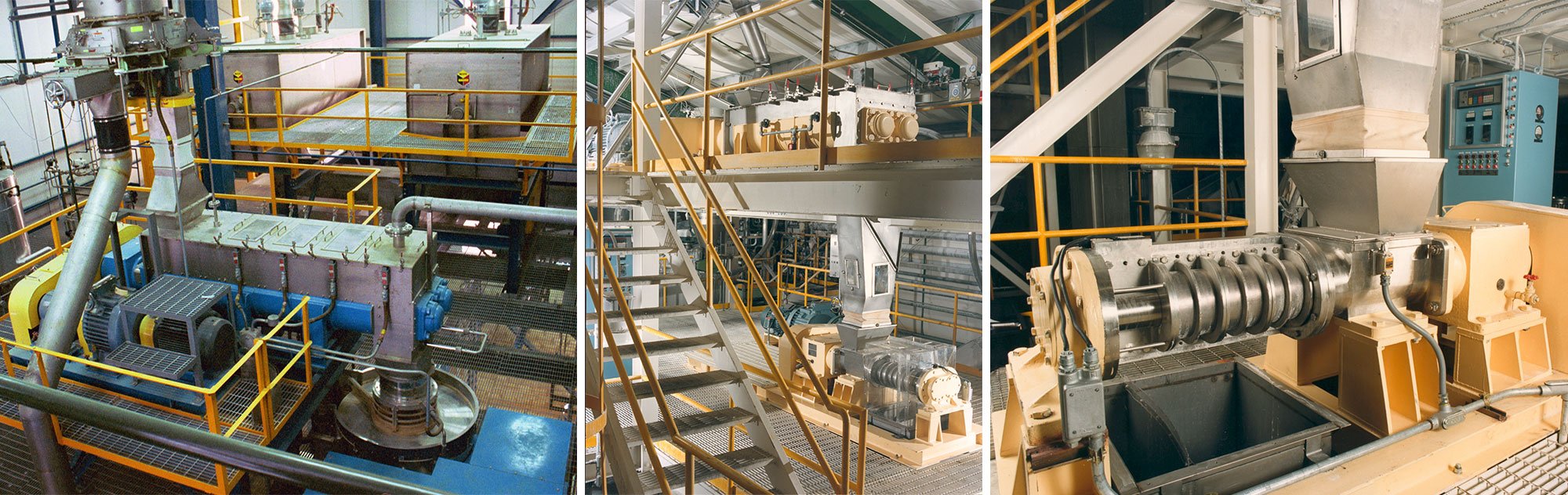
- Home
- Powder Handling
Powder Pelleting Plant
Powder Pelleting Plant
LCI can engineer and provide complete granulation systems which take your product from powder to pellet or sphere, ready for packaging or further processing.
The Powder Pelleting Process
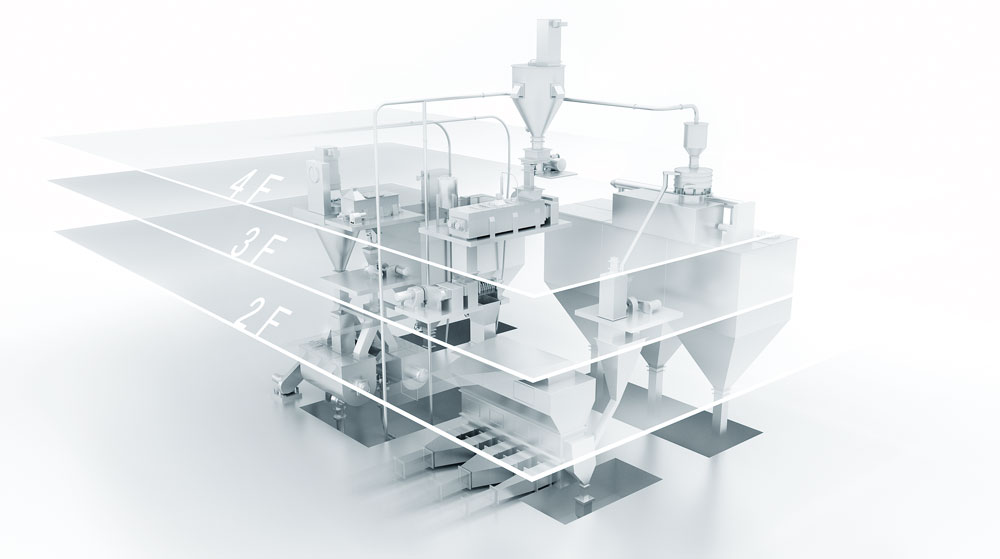
1. Feeding
Circle Feeder – Up to 1.9 m3/min (~68 ft3/min)
The Circle Feeder™ is widely known for its ability to prevent material arching, bridging, and ratholing. The Circle Feeder™ can be manufactured with several outlets for “one to multiple” feeding, which saves on equipment, space, and maintenance costs.
2. Kneading
Continuous Kneader – Up to 480 L (~125 gal) working volume
The Continuous Kneader is a counter rotating twin shaft mixer. The Kneader mixes powders and liquids together continuously and homogeneously, making it ideal for continuous downstream processes that require consistent moisture levels. Can be jacketed for heating or cooling applications.
3. Extrusion
Basket Granulator™ - Lowest pressure extruder – Up to 1500 kg/hr (~3305 lb/hr)
Twin Screw Xtruder™ - Radial Configuration – Up to 1200 kg/hr (~2645 lb/hr)
The Extruder transforms the homogeneous wet mass to produce well-formed cylindrical extrudates of a controlled diameter. The extrudates break off by their own weight and are collected for the next processing step. Depending on the desired end product, the wet extrudates will either be spheronized or dried.
4. Drying and Packaging
The wet extrudates (or spheres) exiting the extruder (or spheronizer) are charged to the inlet of a Continuously Vibrating Fluid Bed Dryer. The dried granules (or spheres) are then discharged to sieving and / or packaging.
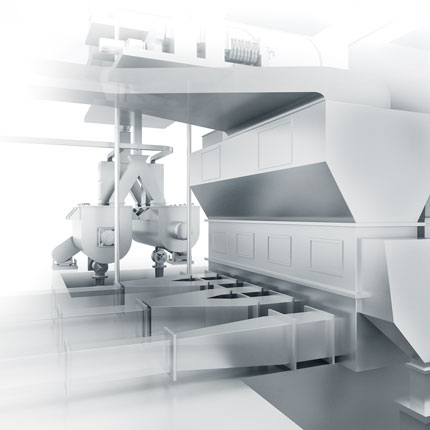