Circle Feeder in the Battery Industry | Answering your Questions on the Technology
The circle feeder is a specialty feeding technology that has been widely used in a variety of industries. LCI has been providing circle feeders for over 25 years. The unique design of the circle feeder allows for the feeding of sticky, fluffy, lumpy, flaky, and fibrous materials without issues of bridging and ratholing.
What Is The Circle Feeder?
The circle feeder is a unique table feeder which is mounted to the bottom of a hopper or silo. Key to the benefit of the design is the much wider inlet possible in comparison to more traditional feeders. Material is charged into the hopper/silo above the feeder and moves to the bottom panel of the circle feeder where a thin flat vane rotates spreading out and moving powder to the periphery of the unit. At the periphery the material is moved over and feed through the discharge port. In this system rate is controlled both by the speed of the vane but also by the clearance height of an internal flow adjustment ring.
The circle feeder is used in a wide variety of industries including but not limited to battery, chemical, agrochemical, plastic, pharmaceutical etc.
Why Use The Circle Feeder? | Installation Advantages
- Reduced height
- Low rotation speed
- Multiple discharge ports
Reduced Height
The wide inlet design of the circle feeder can allow for less vertical space compared to alternative feeders. Range of options for drive arrangement as well that can allow for even further height reduction.
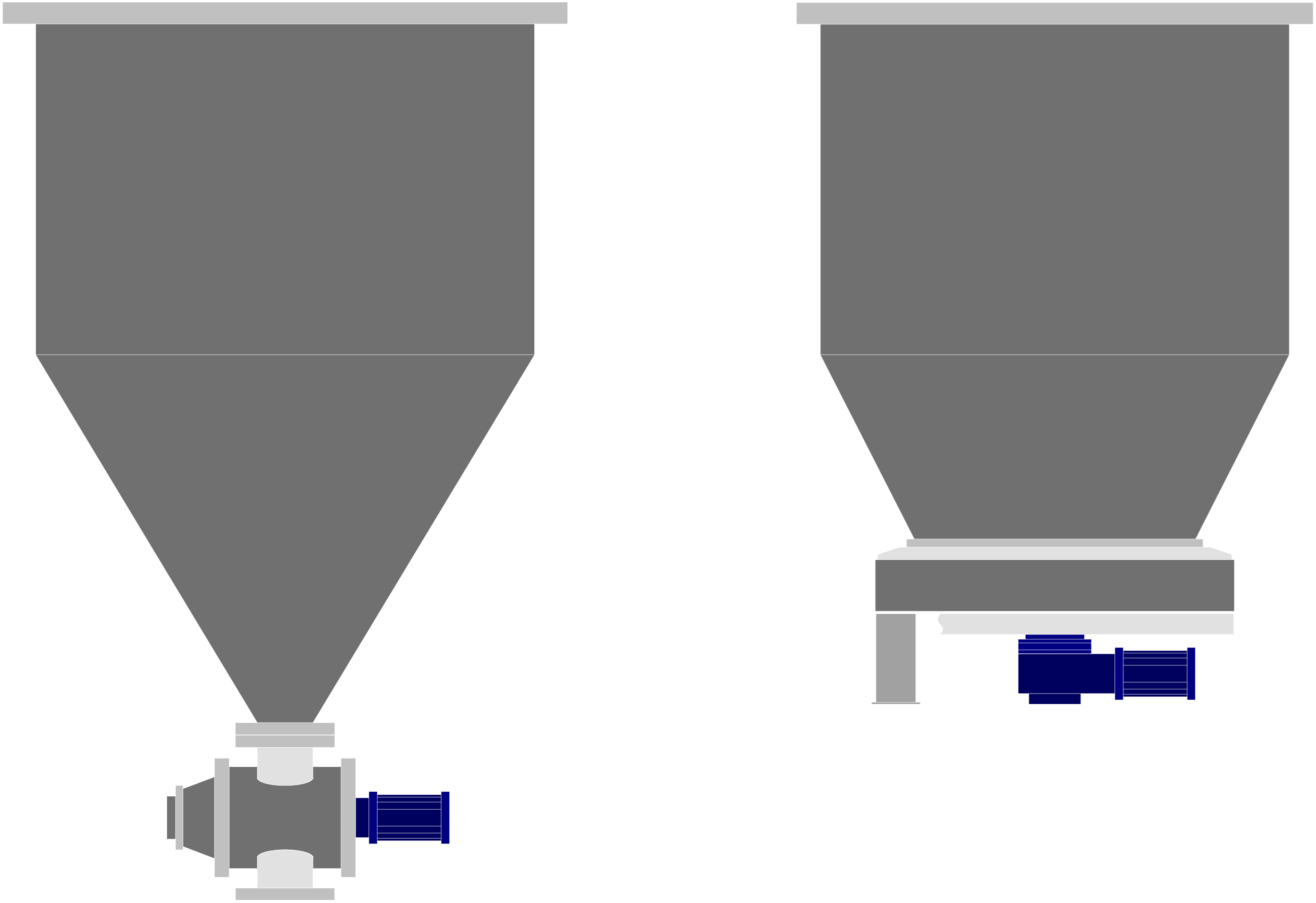
Low Rotation Speed
The rotary vane is moving at very slow speed 0.02-9.2 rpm typically resulting in very low noise and abrasion.
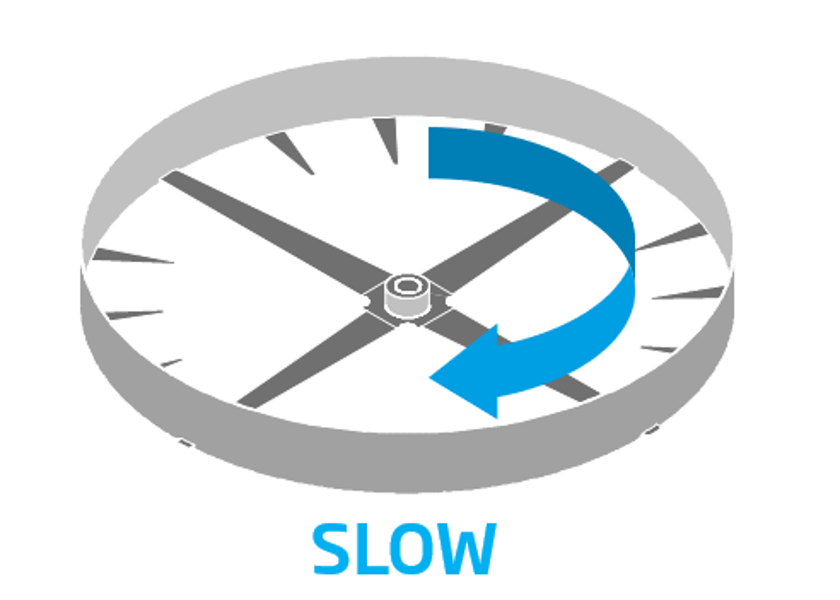
Multiple Discharge Ports
Multiple discharge ports can be incorporated into the design allowing for simultaneous or alternative discharge downstream.
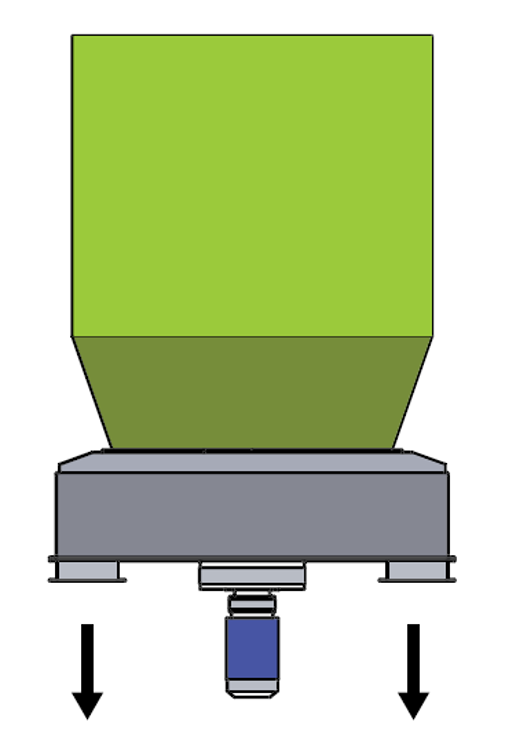
Why Use The Circle Feeder? | The Product Performance Advantages
- Prevents Bridging and Ratholing
- Prevents Segregation
- Consistent Controlled Feeding
Prevents Bridging and Ratholing
The straight walls and wide inlet diameter of the circle feeder are ideal in preventing material from getting below the critical arching diameter where bridging and ratholing occur.
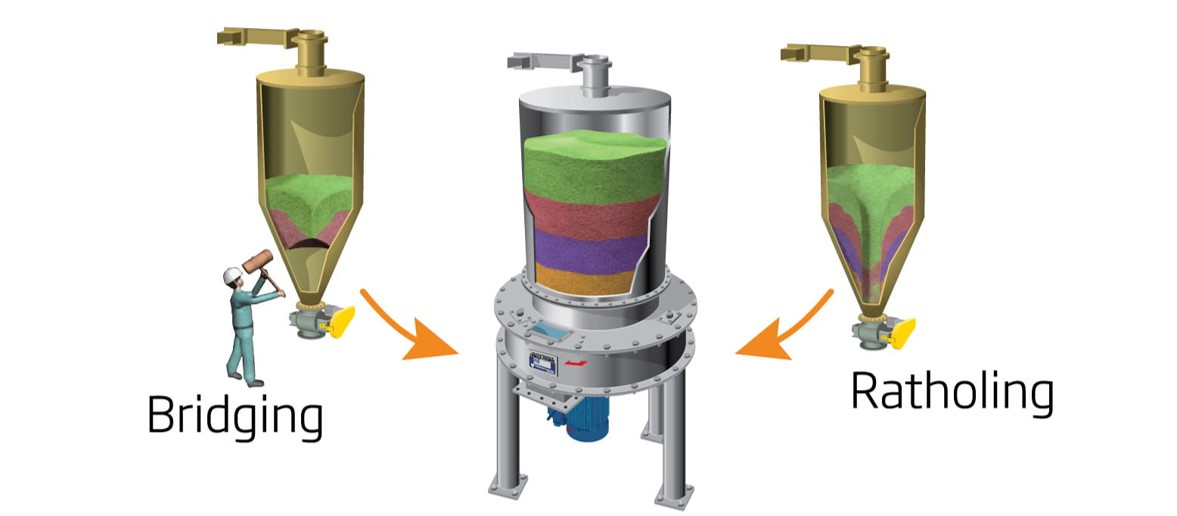
Prevents Segregation
Segregation or the uneven distribution of powders is prevented in the circle feeder because the circle feeder allows for mass flow (first in first out). This can be critical in applications where mixing and drying occur as you are ensured a much more consistent mix and dry time. It also can allow for long term storage without impact to the homogeneity of the product.
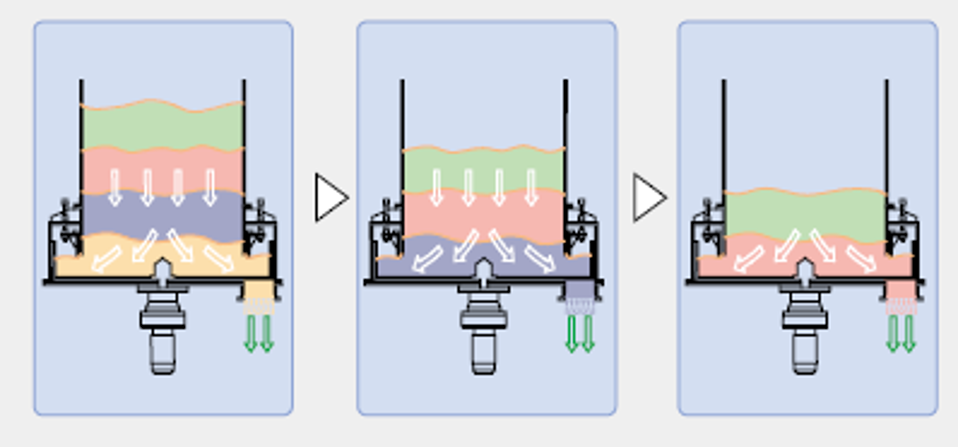
Consistent Controlled Feeding
Flow rate in the circle feeder can be controlled first by the flow adjusting ring height. Essentally the higher the flow adjusting ring setpoint the more clearance there is for flow and the higher the overall rate achieved. The more typical adjustment in a production setting though is done through the setpoint of the rotary vane speed. This can be easy to predict with proper calibration as the trend is generally linear. This speed can also be adjusted through loss in weight or gain in weight systems allowing for more automated and potentially more precise control of feed rate or batching weight.
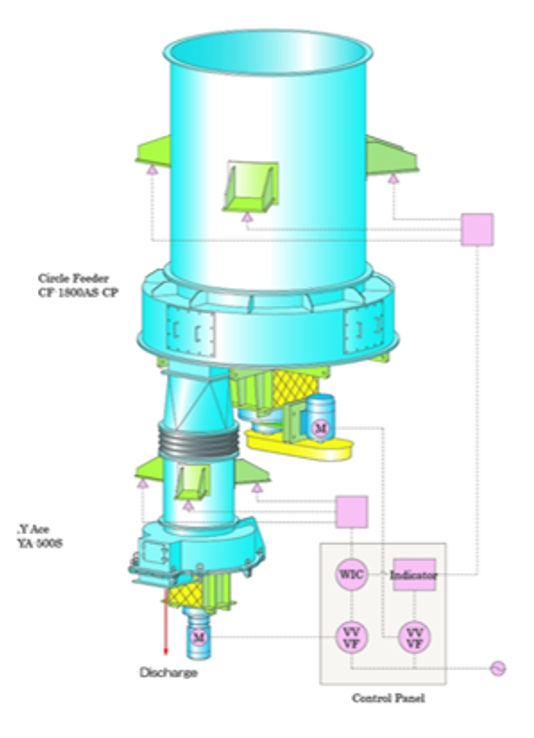
Examples of Circle Feeding Applications
Battery Industry – Cathode and Anode Production
- Cobalt
- Nickel
- Manganese
- Iron Phosphate
- Graphite
- Lithium Titanate
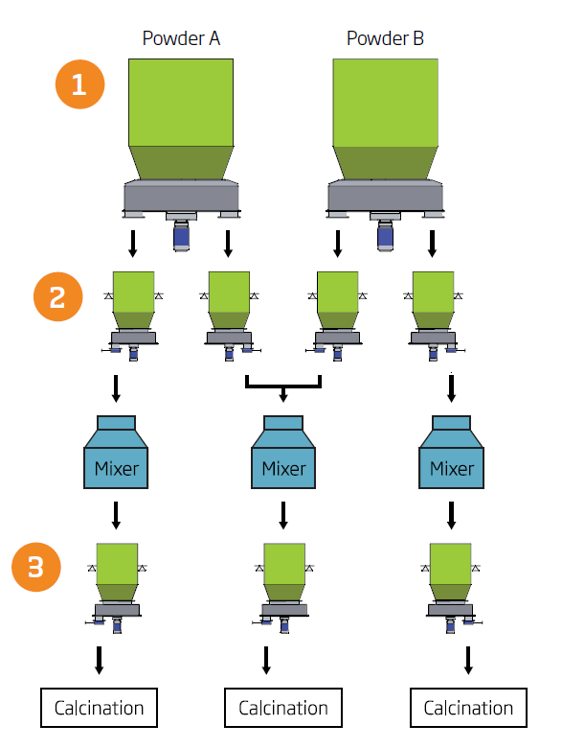
General Chemical
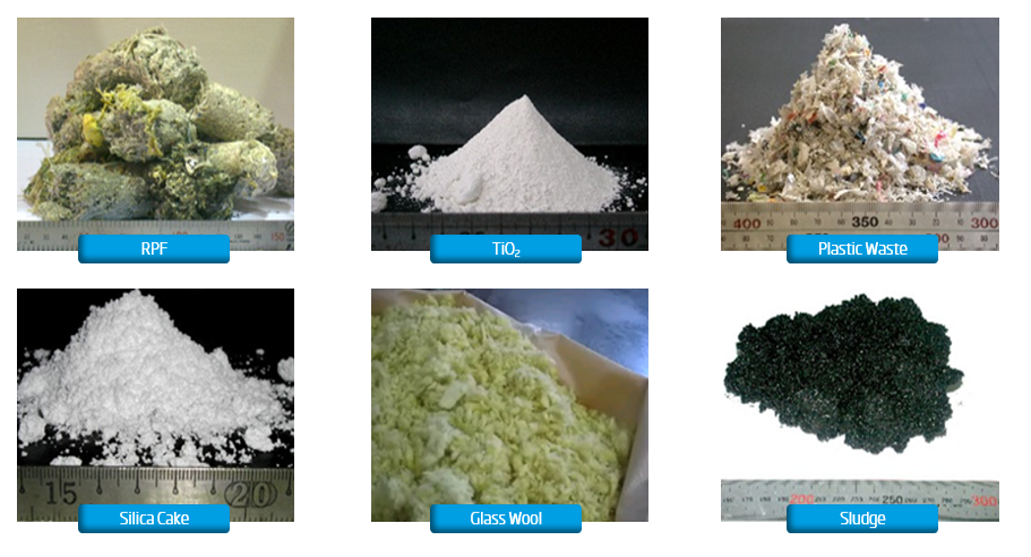
Finding Your Granulation Solution
LCI has a broad range of granulation technology supported by a team of process experts and a test center where you can validate your solution. Would you be interested in testing if the circle feeders is a solution for your flow needs? Speak with an engineer about your process goals to get started on a solution.