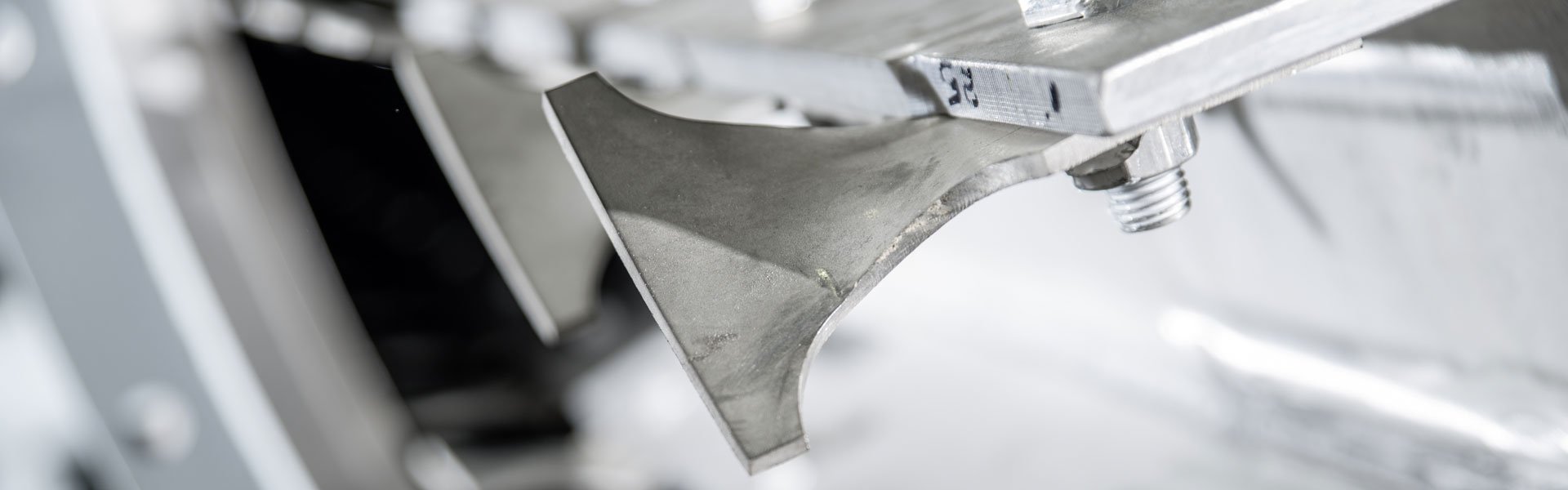
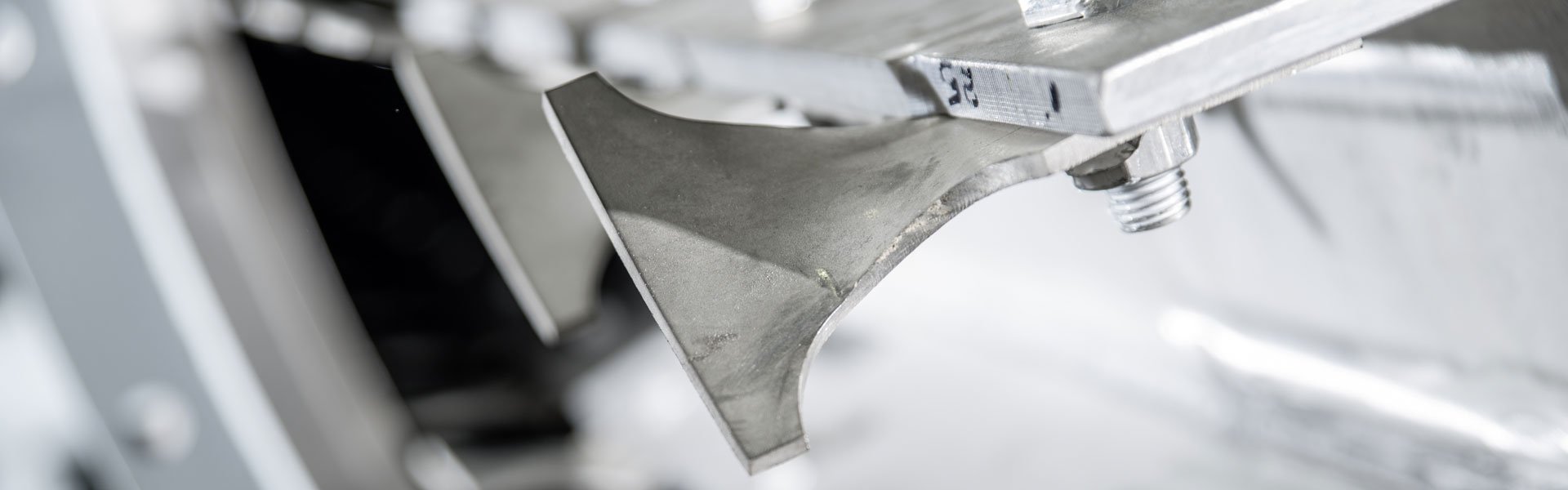
- Home
- Sludge Drying
Thin Film Sludge Dryer
Thin Film Sludge Dryer
Thin Film Sludge Dryer Fast Facts
Thermal sludge drying equipment designed to simply and safely dry dewatered sewage sludge in a sustainable and configurable process.
Sustainable
- Low Energy Usage to mitigate climate change with optional heat recovery to minimize carbon footprint
- Adaptable to Process Changes allowing the system to fit current or future processes
- Low Cost of Ownership including capital, installation, operation, and maintenance
- Heat recovery for beneficial reuse of the heat stream for digester heating, pre-drying or use in other heating processes
Configurable
Accepts any Feed Sludge including:
- Sticky, pasty and liquidly sludges
- Poorly screened sludges
- Poorly dewatered sludges
- Undigested primary and/or secondary sludges with high organic content
- Industrial sludges
- Digested sludges
- Biomass/High Strength Waste sludges
Outputs as variety of dried sludge characteristics:
- Partially or fully Dried Biosolids between 30-95% DS
- Densities typically greater than 40lb/ft3
- Variable dried sludge sizes with low dust content from secondary drying and/or post-product pelletization
Construction and Design can be tailored to:
- Sticky, pasty and liquidly sludges
- Fit a compact building footprint
- Fit existing buildings with small overall footprint or low head space
- Available with multiple condenser options including designs with heat recovery
- Designs with secondary drying for a more compact footprint
Simple
The Dryer requires no back-mixing or extruder systems for feeding as sludge is directly pumped into the dryer. The small exhaust vapor stream lowers electrical use and emissions control requirements.
Single non-heated auger requires:
- No alignment
- No heating fluid
- Designed for the life of the dryer
Automated Operation allows:
- Continuous operation (24 hr/day)
- Limited daily operational hours (8-12 hr/day)
- Quick startup and shutdown (emptying in less than 15 minutes)
Single, simple, bolted blades and preconfigured trolly system allow quick and easy Maintenance at the operation floor level.
Safe
- Designed as an indirect dryer with inert drying atmosphere
- Negative pressure pulls dust and contaminated air into the dryer away from the operational area
Proven
- In service for over 30 years
- Over 100 installations
- In service in the US since 2008
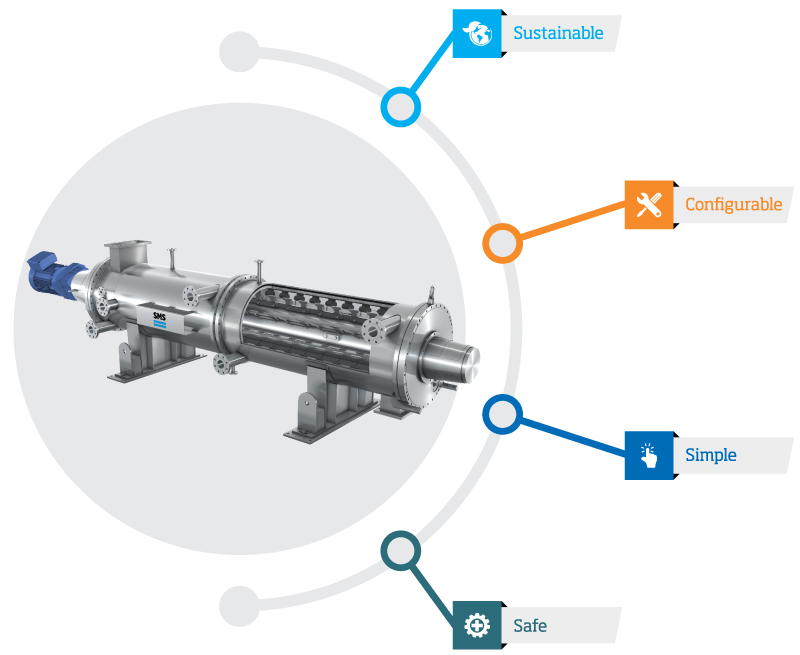
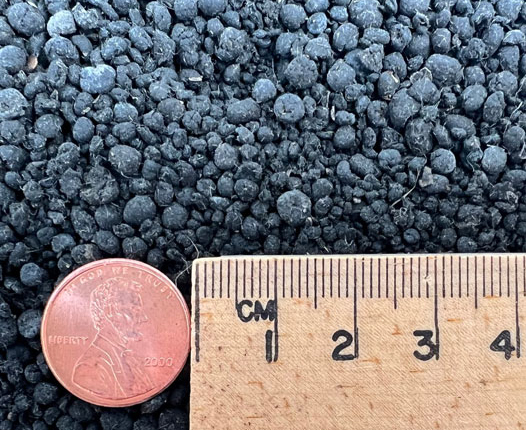
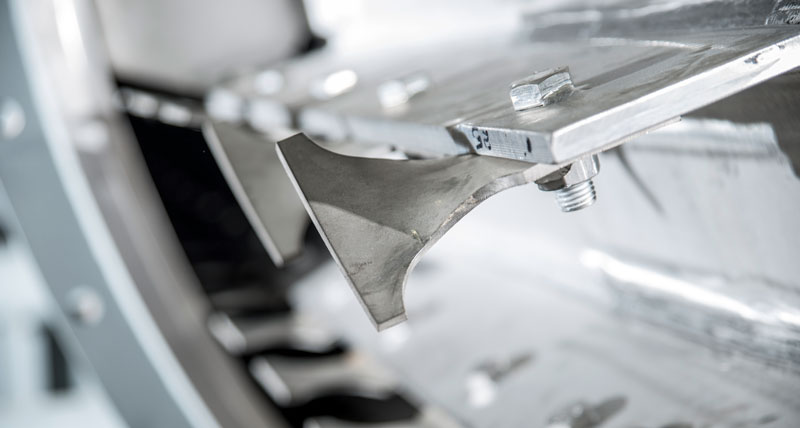
Biosolids - Industries at a Crossroads
In 2015, the U.N. developed 17 Sustainable Development Goals. Chip Pless dives into the industries at a crossroads with biosolids.
Future of Biosolids Disposal
Carbon Sequestration from Biosolids
Why is Sludge Drying Important
What Problems Do Thin Film Sludge Dryers Solve
LCI’s thin film sludge dryers can accept a wide range of sludge types such as digested or undigested sludge, primary and/or secondary sludge, industrial sludge, sludge with high amounts of high strength waste or Biomass, sludge which is poorly dewatered, “sticky” sludges, and more.
Safety
Safety is paramount when drying sludge. Dried sludge is combustible and therefore needs to be treated as such. The highest risk for fire and explosion is generally the combustible dust from the drying process. LCI and our parent company Nederman have vast experience in explosive dust applications and the NFPA (National Fire Protection Association) codes surrounding dust applications.
Efficiency
One of the highest operational cost associated with Sludge Drying is the thermal and electrical energy to dry the material. Increases in efficiency associated with energy consumption can significantly reduce the cost of operating a dryer system. Due to the “Thin Film” design of our dryer, LCI can boast of having one of the highest thermal and electrical efficiencies on the market.
End Product
The product discharged from a drying system is very important as to the end use of the dried material. The characteristics of the end product are different depending on the application the material is used in. LCI’s experience in the granulation market make us a perfect partner to assist in developing a dryer system which can generate the end product the application requires.
Emissions Control
Dryers release moisture which contains different compounds which must be considered. With ever increasing air standards it is important to understand and treat the moisture released from a dryer system. LCI’s parent company, Nederman, is know as the “Clean Air Company” and our sister company Mikropul specializes in Industrial Air Filtration so LCI has the experience to assist in the emissions control requirements of drying applications.
Common Processes Supported by Thin Film Sludge Dryers
- Agricultural (Beneficial Reuse)
- Mono-Sludge Incineration
- Co-Incineration with Solid Waste
- Gasification
- Pyrolysis
- Landfill Disposal
Downloadable Documents
Thin Film Thermal Sludge Dryer Brochure
Thin Film Thermal Sludge Dryer Questionnaire