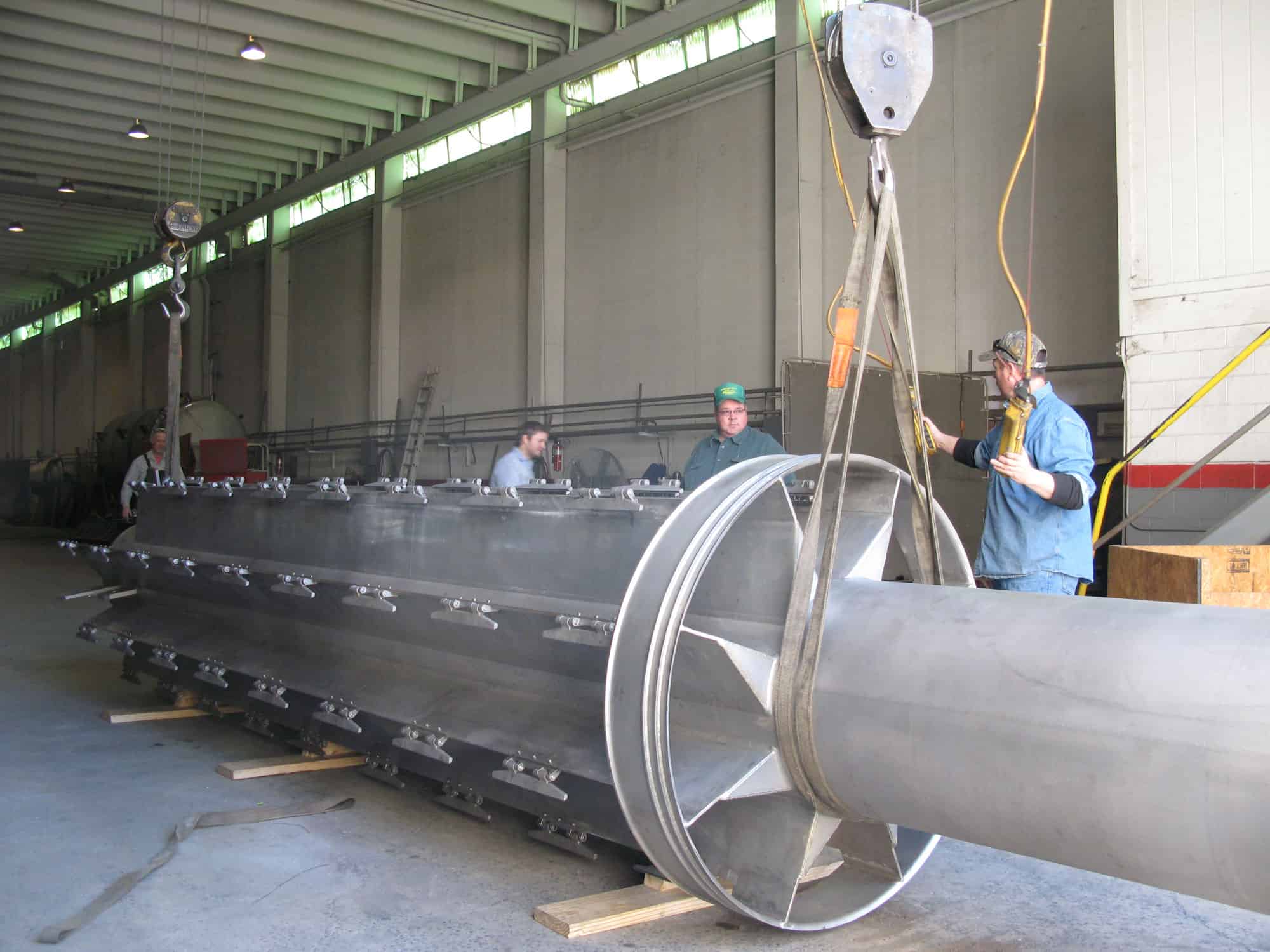
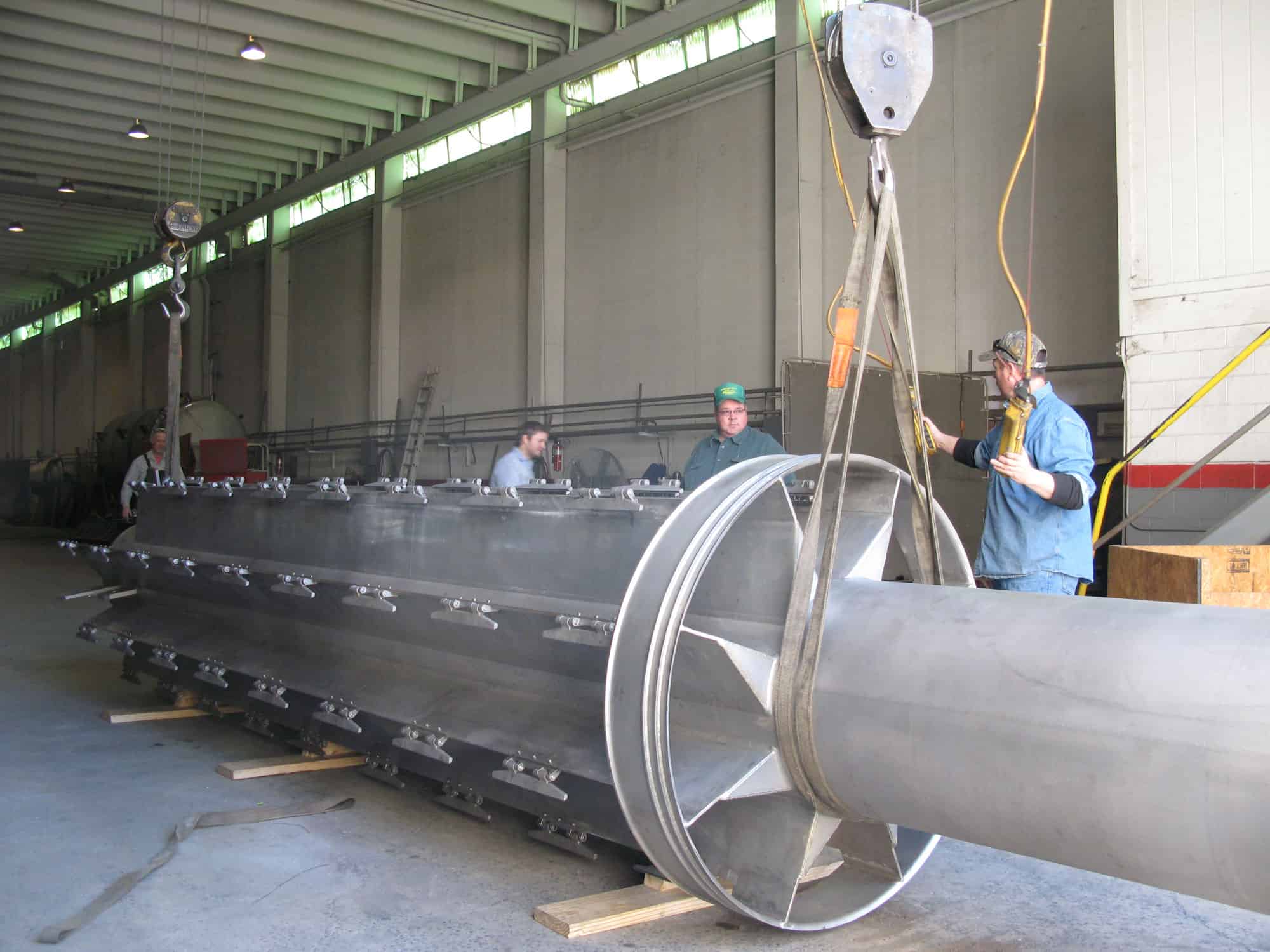
- Home
- Evaporation
- Thin Film Dryers
Thin Film Dryer How It Works
Thin Film Dryers - How It Works
Product enters above the heated zone and is evenly distributed over the unit's inner surface by the rotor. Hinged blade elements transport the viscous material down the thermal surface and promote heat transfer.
Volatile components are rapidly evaporated and flow counter-currently to the solid/liquid flow through the unit. Vapors are ready for condensing or subsequent processing upon existing the dryer.
As the volatiles are evaporated, the solids eventually stop flowing and create masses which the thin film dryer blades then eject from the wall. The free-flowing solids then fall down the remainder of the evaporator to the discharge section. For horizontal dryers, segmented blades are used to push the solids towards the discharge section.
Nonvolatile components are discharged at the bottom of the thin film dryer with a specially-designed discharge section. Dryers typically use special rotary or spherical disc valves for solids discharge handling. The solids can also be directly discharged to a bin hopper or vessel depending on the process requirements.
The dryers are indirectly heated by steam or hot oil and can be operated semi-batch wise or continuously.
Its relative short residence time and open, low pressure-drop configuration allow continuous, reliable processing of many heat-sensitive, viscous materials without product degradation.