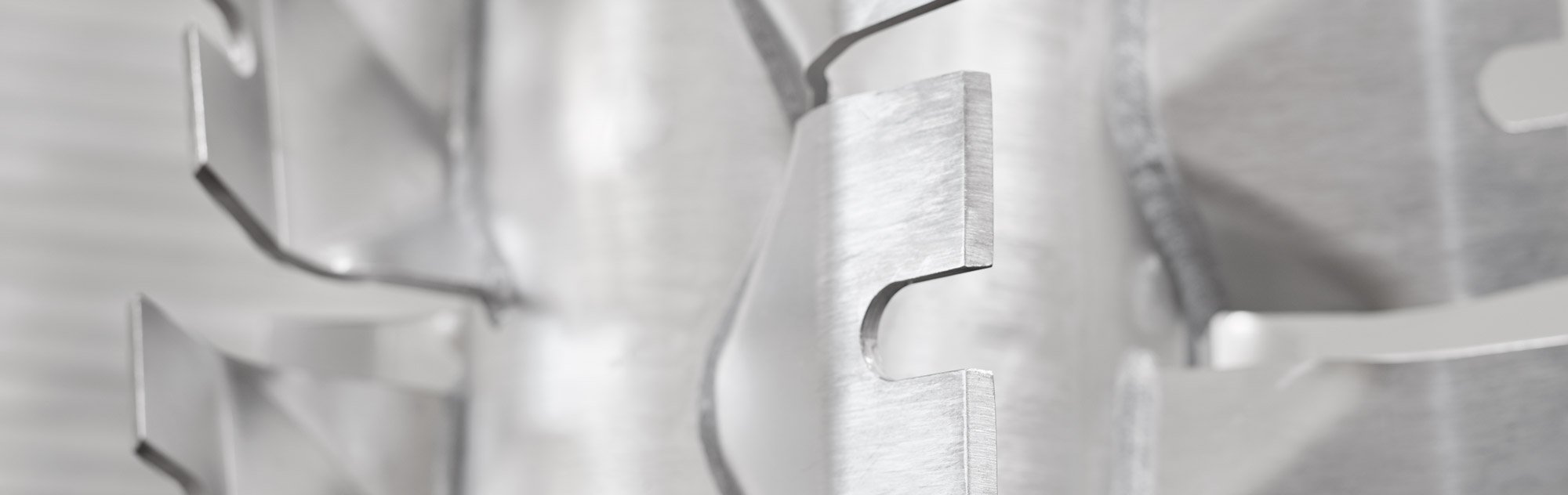
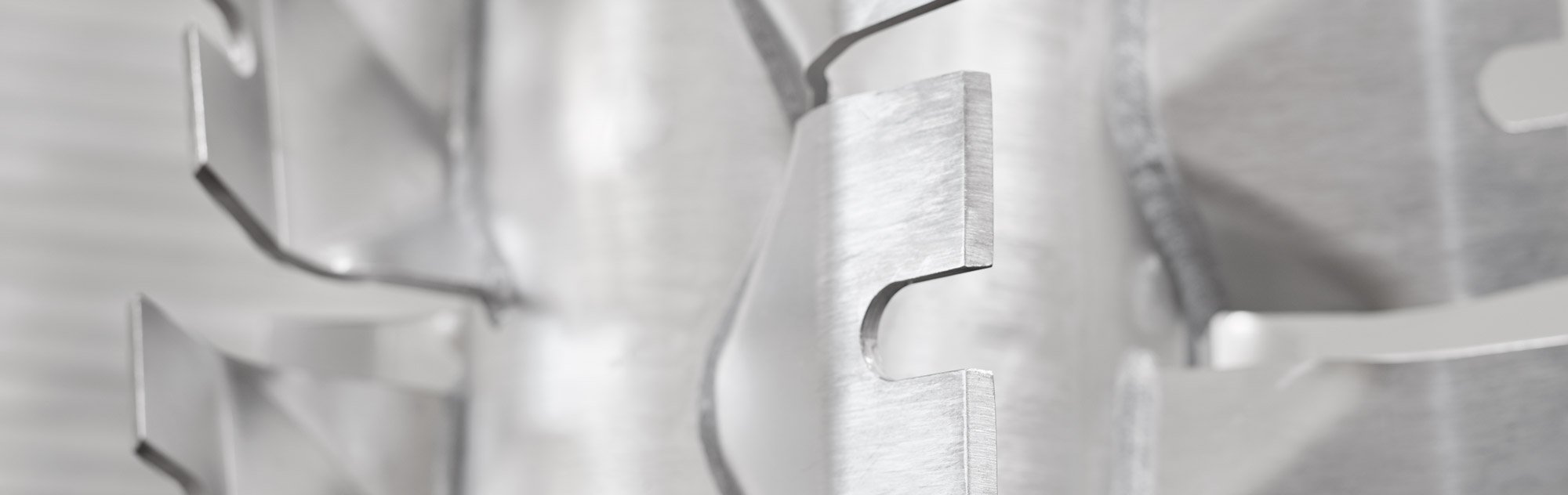
Purify Silicone Efficiently and to the Highest Quality
Thin film evaporation technology presents several advantages in the process of silicone purification. Notably, this method offers rapid removal of volatile components to parts-per-million levels within a scalable and environmentally friendly equipment package.
Thin film evaporation technology presents several advantages in the process of silicone purification. Notably, this method offers rapid removal of volatile components to parts-per-million levels within a scalable and environmentally friendly equipment package.
High Efficiency in Separation
Thin film evaporation allows for the effective removal of volatile impurities, including silicone cyclics, from polysiloxane oils and silicone gums. This purification step is crucial for producing silicones that are safe for use in a wide range of consumer products. The technology's ability to operate under vacuum conditions enhances the efficiency of volatile component removal, ensuring that the final product meets stringent purity specifications.
Handling of Highly Viscous Materials
One of the unique features of thin film evaporators is their capacity to process highly viscous products without degradation. Thin film evaporators can process liquids with viscosities up to 10 million centipoise (cP), demonstrating their robustness in handling thick silicone oils and gums.
This is particularly important for silicone grades where the material's viscosity can pose challenges for traditional purification technologies. The agitated thin film evaporator employs a combination of high turbulence and rapid surface renewal, utilizing a proprietary blade design, facilitating the handling of viscous silicones effectively.
with Thin Film Evaporation
Temperature-Sensitive Processing
The sensitivity of silicones to temperature during purification necessitates a gentle processing approach. Operating at internal pressures as low as 0.002 mbar, the thin film evaporator significantly reduces the heating temperature needed for the process. When combined with an extremely short residence time (less than 3 minutes), the heat history of the silicone material is reduced, preventing degradation.
Scalability and Environmental Considerations
The design of thin film evaporators supports scalability, allowing for the purification process to be adjusted and expanded according to production demands. Moreover, the technology's environmentally friendly features, such as the reduced energy consumption and minimized waste production, align with the growing emphasis on sustainable manufacturing practices.
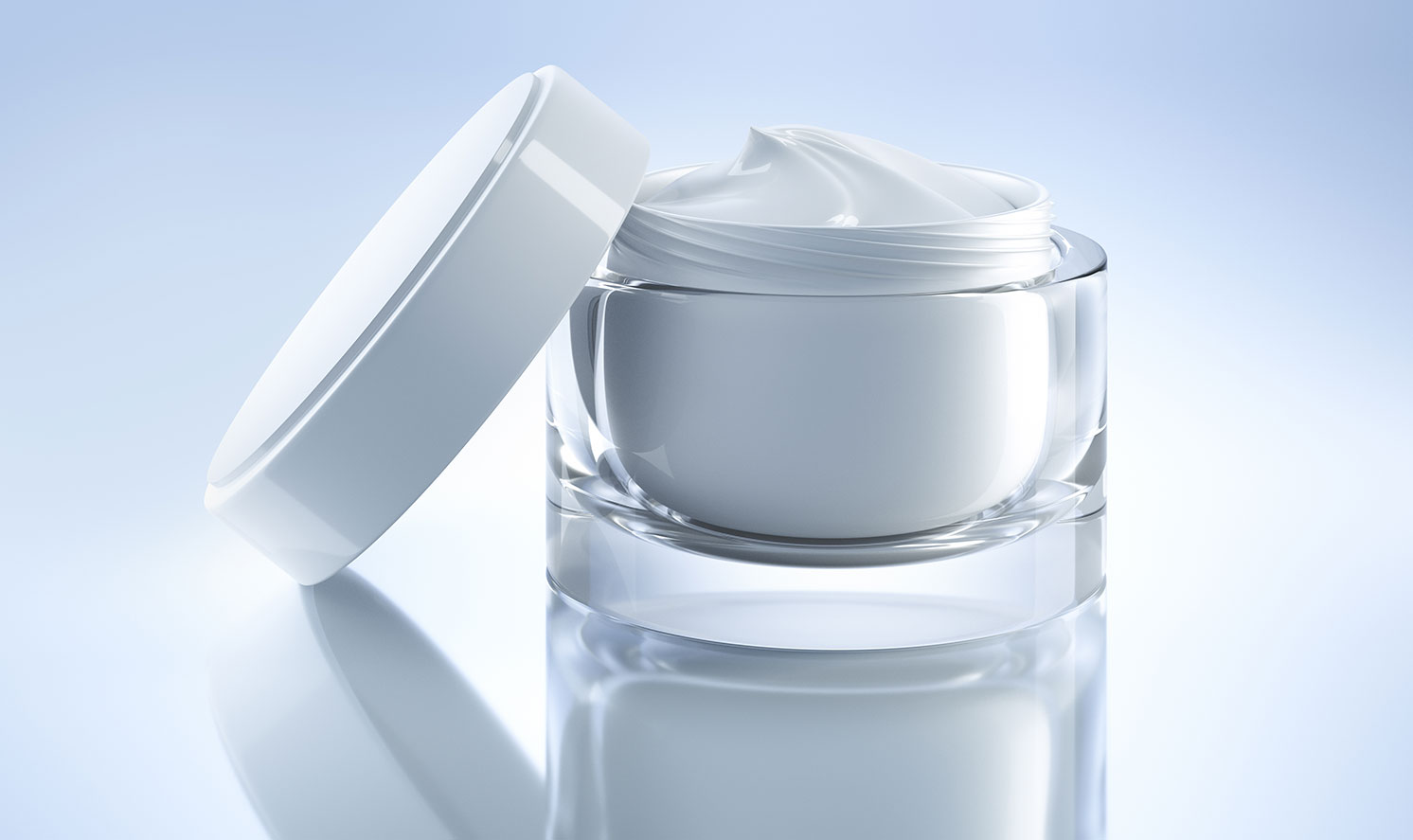
Enhanced Product Quality and Safety
By removing impurities to safe parts-per-million (PPM) levels, thin film evaporation ensures that the final product meets safety and regulatory compliance for consumer silicone products. This is critical for manufacturers aiming to produce consumer products that are not only effective but also safe for use.
Continuous Processing and Increased Production Rates
The continuous operation mode of thin film evaporators leads to increased production rates, eliminates times,as well as enhanced process efficiency. This continuous processing capability is essential for meeting the high demand for purified silicones in various industries, including healthcare, cosmetics, and electronics.
Thin film evaporation in silicone purification offers a multitude of advantages, from improved efficiency and handling of viscous materials to the assurance of high-quality and safe products. The technology's adaptability, combined with its environmental benefits, makes it an invaluable asset in the modern manufacturing landscape, enabling silicone producers to achieve their quality and production goals while adhering to sustainability principles.
Need to test your concept? Contact LCI and schedule a test. The LCI Test Center, located in Charlotte, NC,is fully staffed and equipped with laboratory and pilot scale equipment. Our engineers can arrange laboratory and pilot-scale tests to evaluate customer products and develop processes.
Contact us today to see how we can help you improve your silicone purification process.